8 layer Rigid Flex Pcb 1+6+1 stackup Special Process Flying Tail Structure
How Capel's 8 layer Rigid Flex Pcb 1+6+1 stackup Special Process Flying Tail Structure Provides Reliability Solutions for Our Costomers
-Capel with 15 years of professional technical experience-
Here we will introduction an exciting and innovative development in the electronics industry - 8-layer rigid-flex PCB with 1+6+1 stack-up and a special process called flying tail structure. The combination of advanced manufacturing techniques and unique design features enables PCBs to overcome limitations and meet the demands of modern electronic applications. Join us as we explore every aspect of this cutting-edge technology.
First, let’s understand what rigid-flex is and why it has gained popularity in recent years. Rigid-flex board is a hybrid circuit board that combines a rigid substrate and a flexible substrate. This unique construction increases functionality and reliability, making it a suitable choice for a variety of applications.
The 8-layer stackup of a PCB refers to the number of layers of conductive material and insulating layers embedded within the board. A 1+6+1 stack specifically means there is one rigid layer on the top and bottom, while the remaining six layers are flexible. This stack-up configuration provides the advantages of rigid and flexible PCBs while eliminating their respective disadvantages.
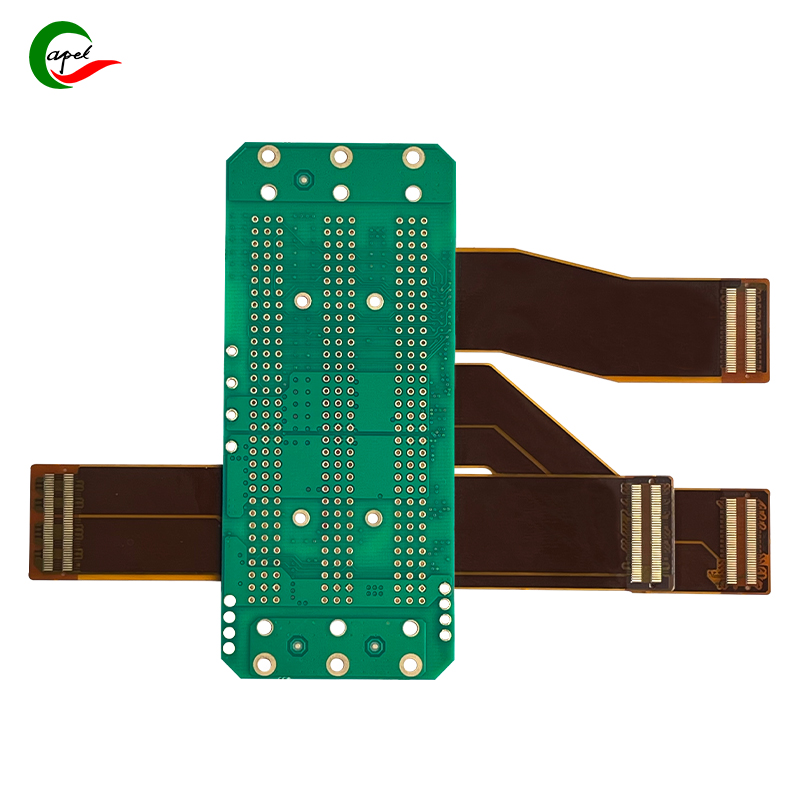
However, what is unique about this particular PCB is the flying tail structure, which is achieved through a special manufacturing process. The flying tail structure is the integration of flexible circuits between rigid layers, allowing for seamless integration of different components. This unique design allows for better signal transmission, lower impedance and improved mechanical stability. It also enhances the overall flexibility and durability of the PCB, making it more resistant to mechanical stress and vibration.
Let’s take an in-depth look at the specific advantages of the 8-layer rigid-flex board with a 1+6+1 stacked flying tail structure. First, the combination of rigid and flexible layers provides a compact design, reducing form factor and increasing functionality. This is particularly beneficial for space-constrained industries such as aerospace, medical devices and wearable technology.
In addition, the flying tail structure improves signal integrity and reduces the risk of electromagnetic interference (EMI). The flexible circuit acts as an excellent signal carrier, while the rigid layer provides adequate shielding. This makes 8-layer rigid-flex PCBs ideal for high-speed and high-frequency applications where data transmission and integrity are critical.
In addition, the special manufacturing process of the flying tail structure ensures the reliability and life of the PCB. Because flexible circuits are integrated within rigid layers, they are protected from external factors such as moisture, dust, and heat. This additional protection enhances the overall robustness of the PCB, making it suitable for challenging environments and extending its service life.
As with any technological advancement, there are some considerations to keep in mind when using an 8-layer rigid-flex PCB with a 1+6+1 stackup and flying tail construction. First, the design and manufacturing processes involved can be complex and require specialized knowledge. Working with an experienced PCB manufacturer who specializes in rigid-flex technology is critical to ensuring the best results.
Additionally, the cost of producing these PCBs can be higher compared to traditional rigid or flexible circuits. However, for many industries and applications, the benefits provided (such as space savings, improved signal integrity, and enhanced durability) outweigh the initial investment.
In summary,the integration of 8-layer rigid-flex boards with 1+6+1 stacks and flying tail structures is a remarkable development in the electronics industry. The combination of cutting-edge technology and advanced manufacturing processes paves the way for more compact, reliable and high-performance electronic devices. As the demand for smaller and more powerful electronic products continues to grow, 8-layer rigid-flex boards with flying tail structures will undoubtedly play an important role in shaping the future of electronic applications.
Capel Flexible PCB & Rigid-Flex PCB Process Capability
Category | Process Capability | Category | Process Capability |
Production Type | Single layer FPC / Double layers FPC Multi-layer FPC / Aluminum PCBs Rigid-Flex PCB |
Layers Number | 1-30 layers FPC 2-32 layers Rigid-FlexPCB 1-60 layers Rigid PCB HDI Boards |
Max Manufacture Size | Single layer FPC 4000mm Double layers FPC 1200mm Multi-layers FPC 750mm Rigid-Flex PCB 750mm |
Insulating Layer Thickness |
27.5um /37.5/ 50um /65/ 75um / 100um / 125um / 150um |
Board Thickness | FPC 0.06mm - 0.4mm Rigid-Flex PCB 0.25 - 6.0mm |
Tolerance of PTH Size |
±0.075mm |
Surface Finish | Immersion Gold/Immersion Silver/Gold Plating/Tin Plating/OSP |
Stiffener | FR4 / PI / PET / SUS / PSA/Alu |
Semicircle Orifice Size | Min 0.4mm | Min Line Space/ width | 0.045mm/0.045mm |
Thickness Tolerance | ±0.03mm | Impedance | 50Ω-120Ω |
Copper Foil Thickness | 9um/12um / 18um / 35um / 70um/100um | Impedance Controlled Tolerance |
±10% |
Tolerance of NPTH Size |
±0.05mm | The Min Flush Width | 0.80mm |
Min Via Hole | 0.1mm | Implement Standard |
GB / IPC-650 / IPC-6012 / IPC-6013II / IPC-6013III |
Capel do customize Flexible Circuit Board with 15 years of experience with our professionalism
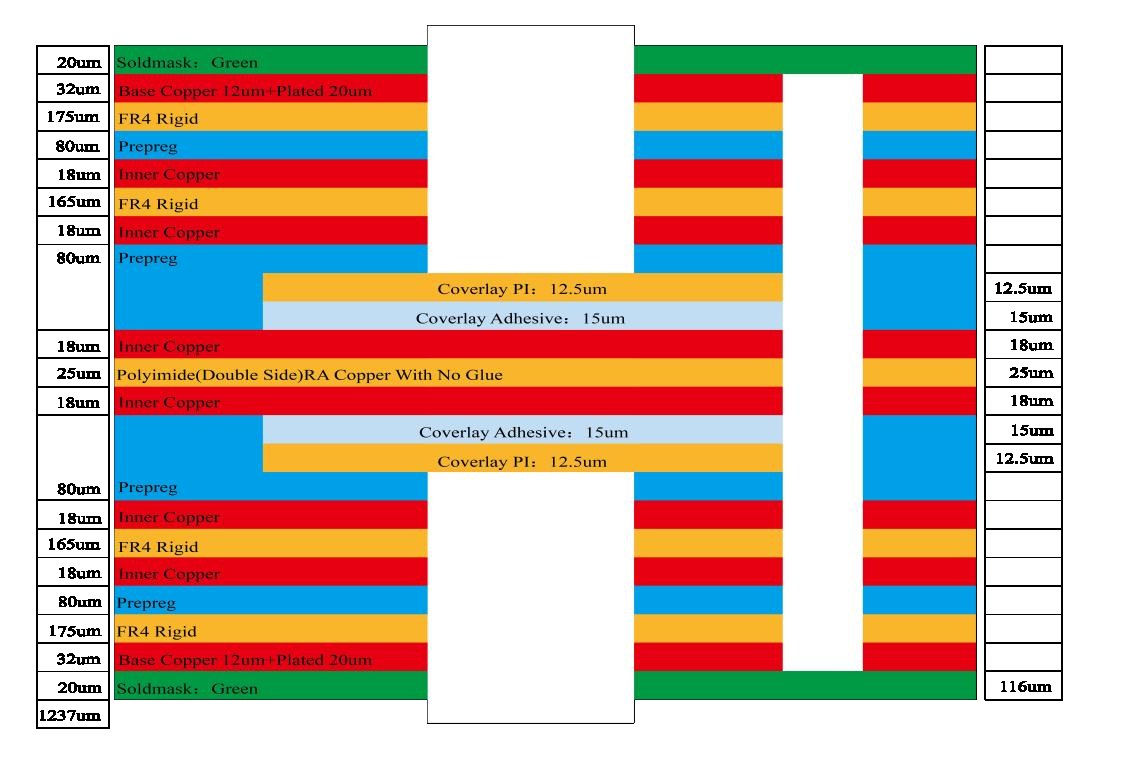
8 Layers Rigid flexible Pcb stackup
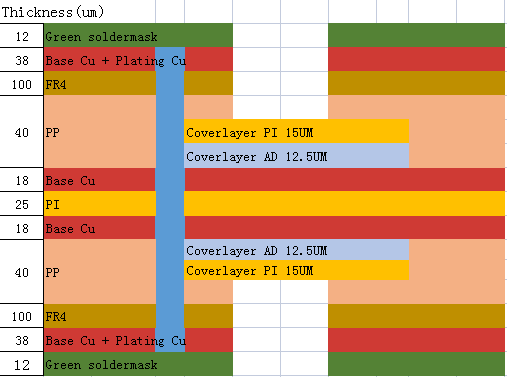
4-layers Rigid-Flex PCB
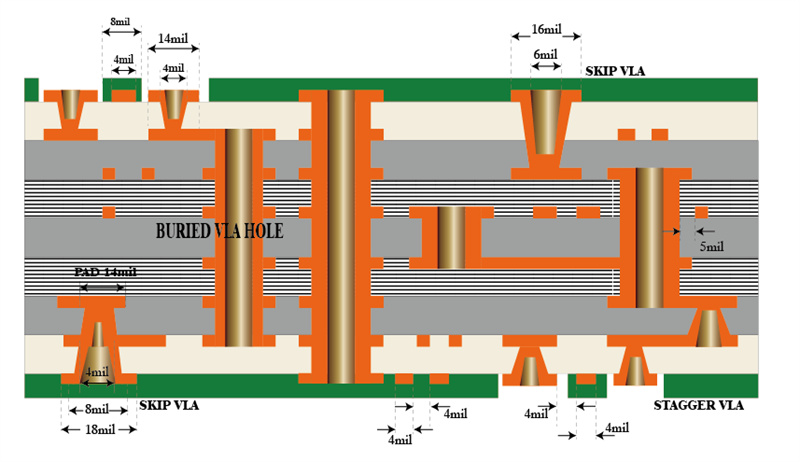
8 layer HDI PCBs
Testing and Inspection Equipment
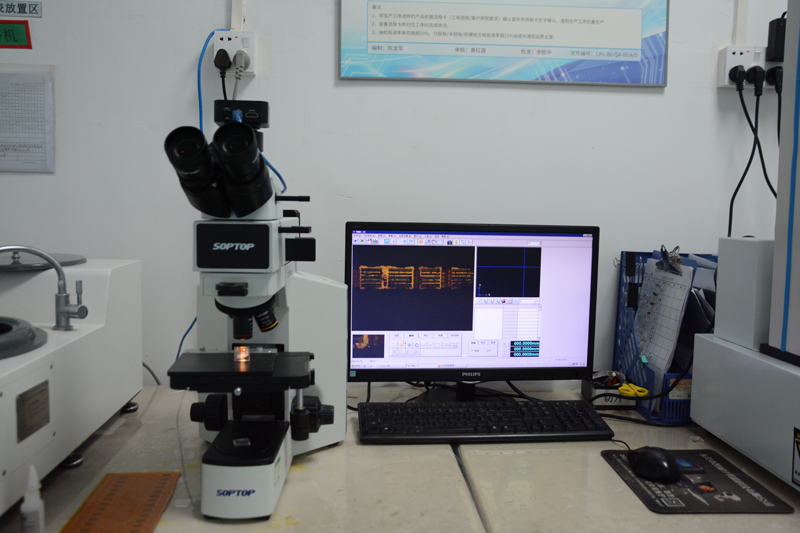
Microscope Testing
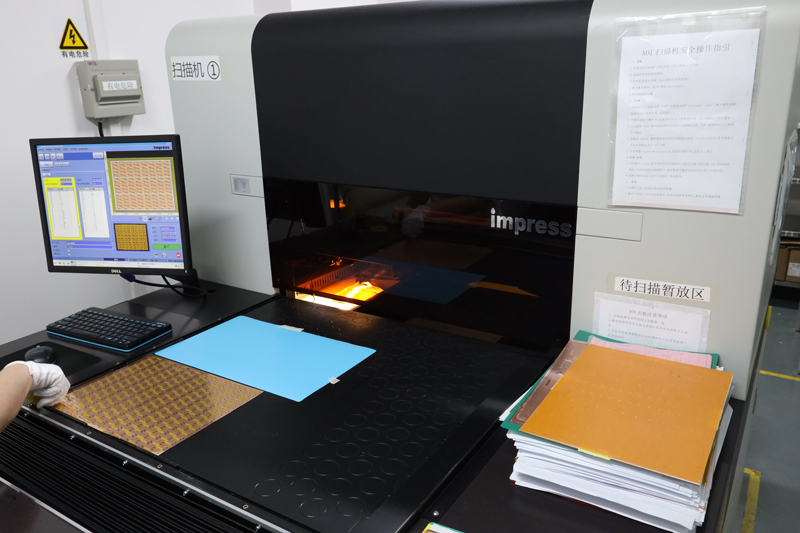
AOI Inspection
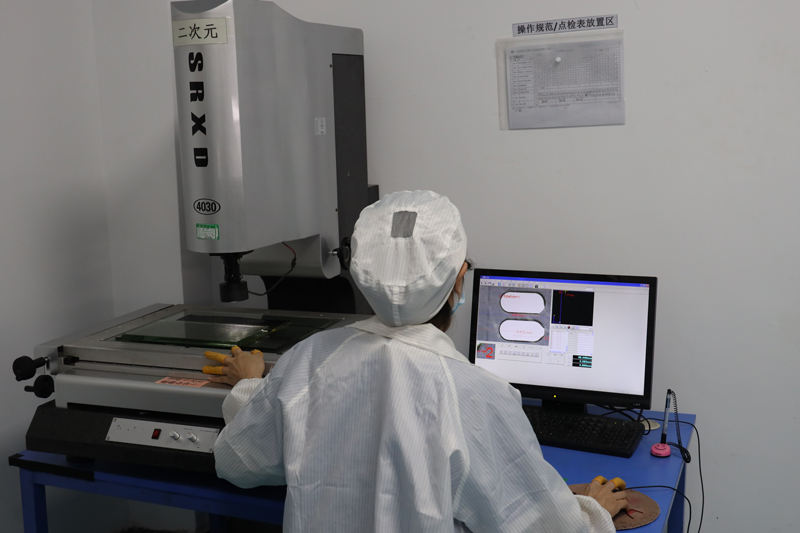
2D Testing
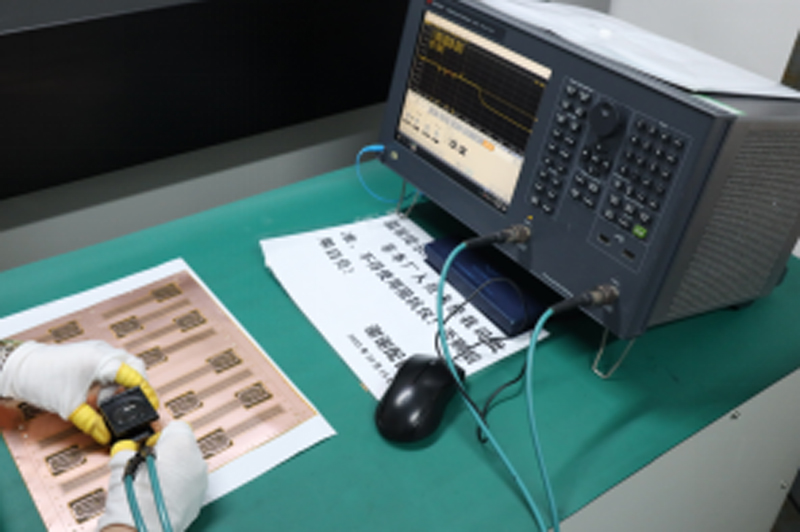
Impedance Testing
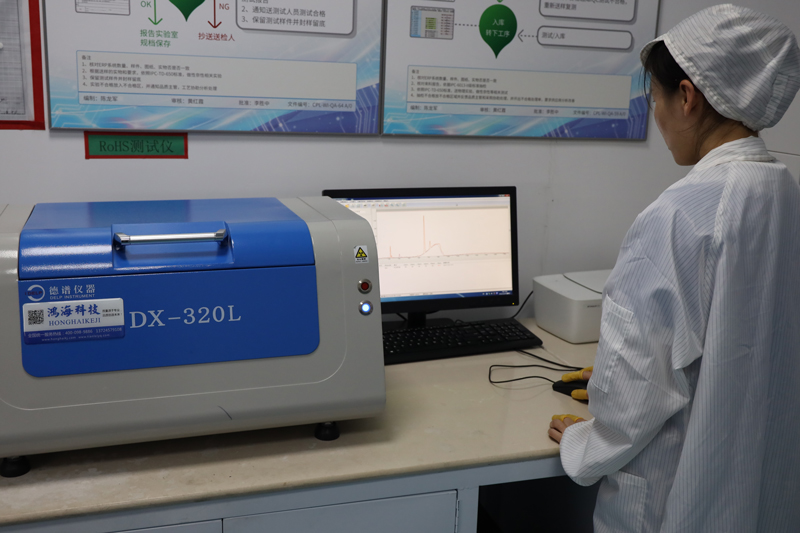
RoHS Testing
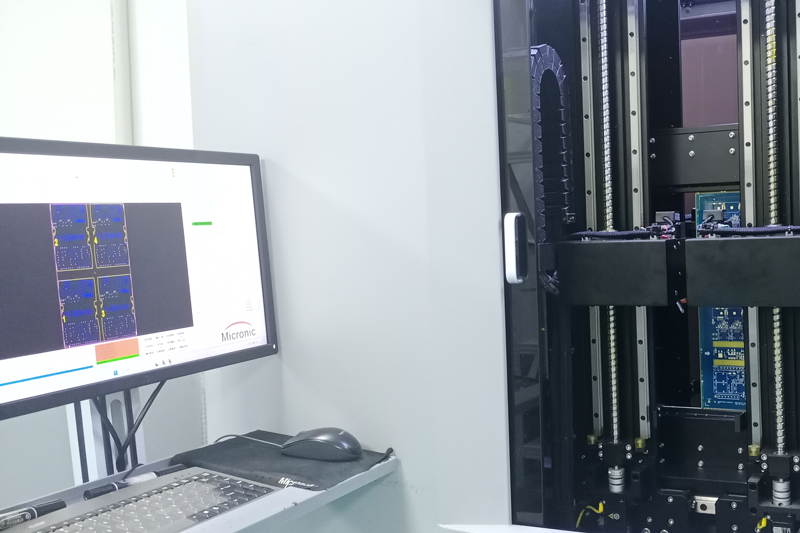
Flying Probe
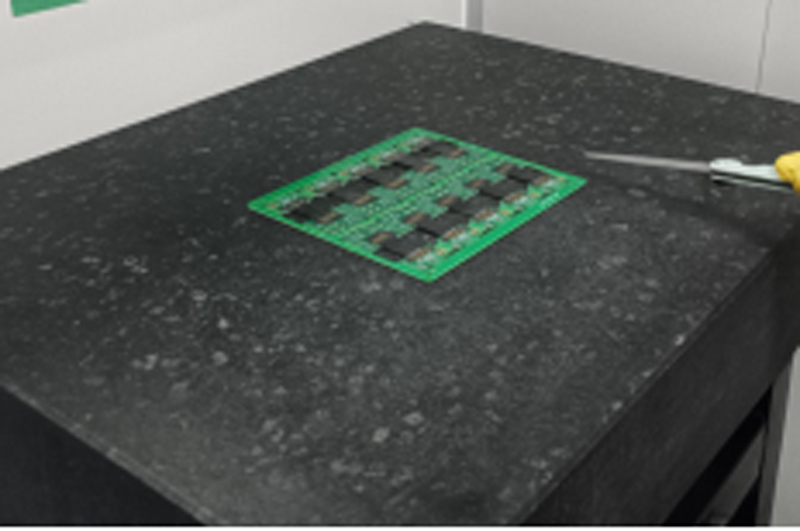
Horizontal Tester
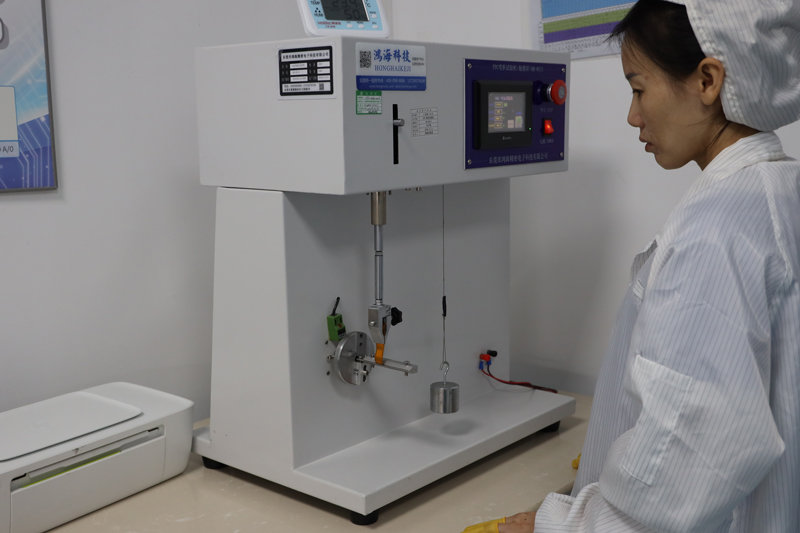
Bending Teste
Capel customized PCB Service with 15 years of experience
- Owning 3 factories for Flexible PCB&Rigid-Flex PCB, Rigid PCB, DIP/SMT Assembly;
- 300+Engineers Provide technical support for Pre-sales and after-sales online;
- 1-30 layers FPC, 2-32 layers Rigid-FlexPCB, 1-60 layers Rigid PCB
- HDI Boards, Flexible PCB (FPC), Rigid-Flex PCBs, Multilayer PCBs, Single-sided PCB, Double-Sided Circuit Boards, Hollow Boards, Rogers PCB, rf PCB, Metal Core PCB, Special Process Boards, Ceramic PCB, Aluminum PCB, SMT & PTH Assembly, PCB Prototype Service.
- Provide 24-hour PCB Prototyping service,Small Batches of circuit boards will be delivered in 5-7 days, Mass Production of PCB boards will be delivered in 2-3 weeks;
- Industries we service: Medical Devices, IOT, TUT, UAV, Aviation, Automotive, Telecommunications, Consumer Electronics, Military, Aerospace, Industrial Control, Artificial Intelligence, EV, etc…
- Our Production Capacity:
FPC and Rigid-Flex PCBs production capacity can reach more than 150000sqm per month,
PCB production capacity can reach 80000sqm per month,
PCB Assembling capacity at 150,000,000 components per month.
- Our teams of engineers and researchers are dedicated to fulfilling your requirements with precision and professionalism.
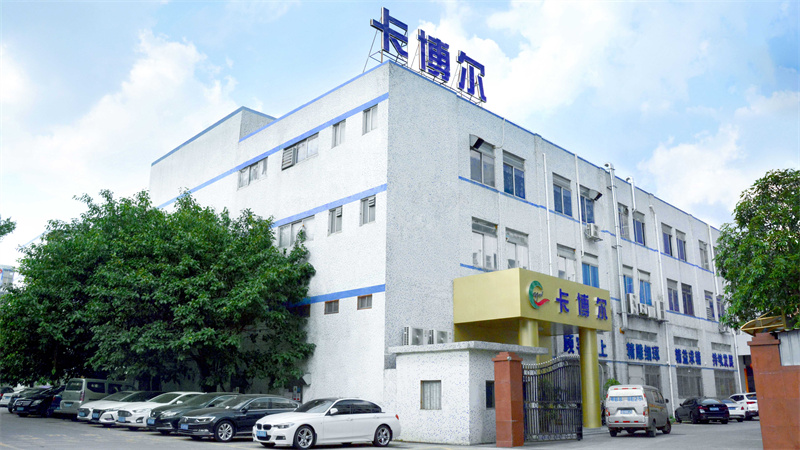
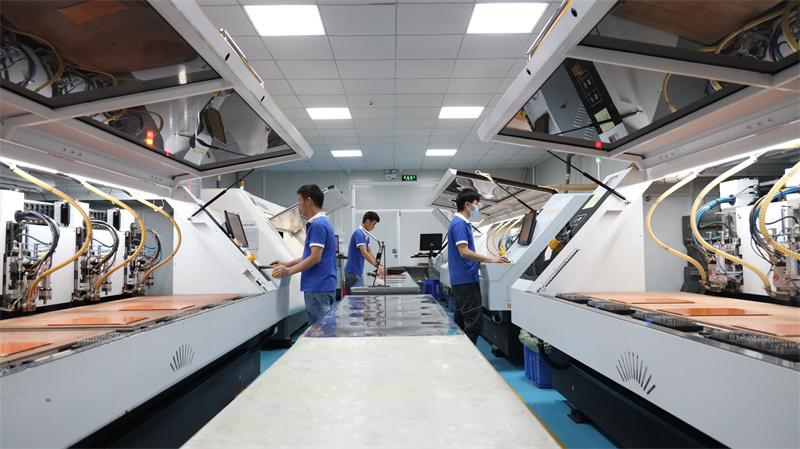
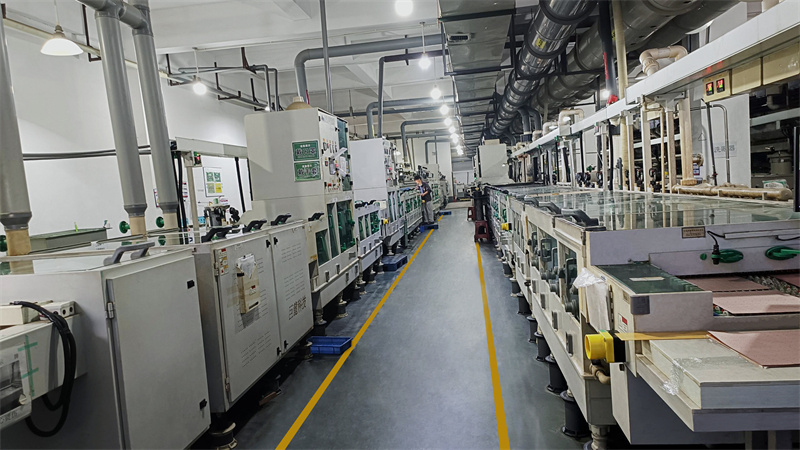
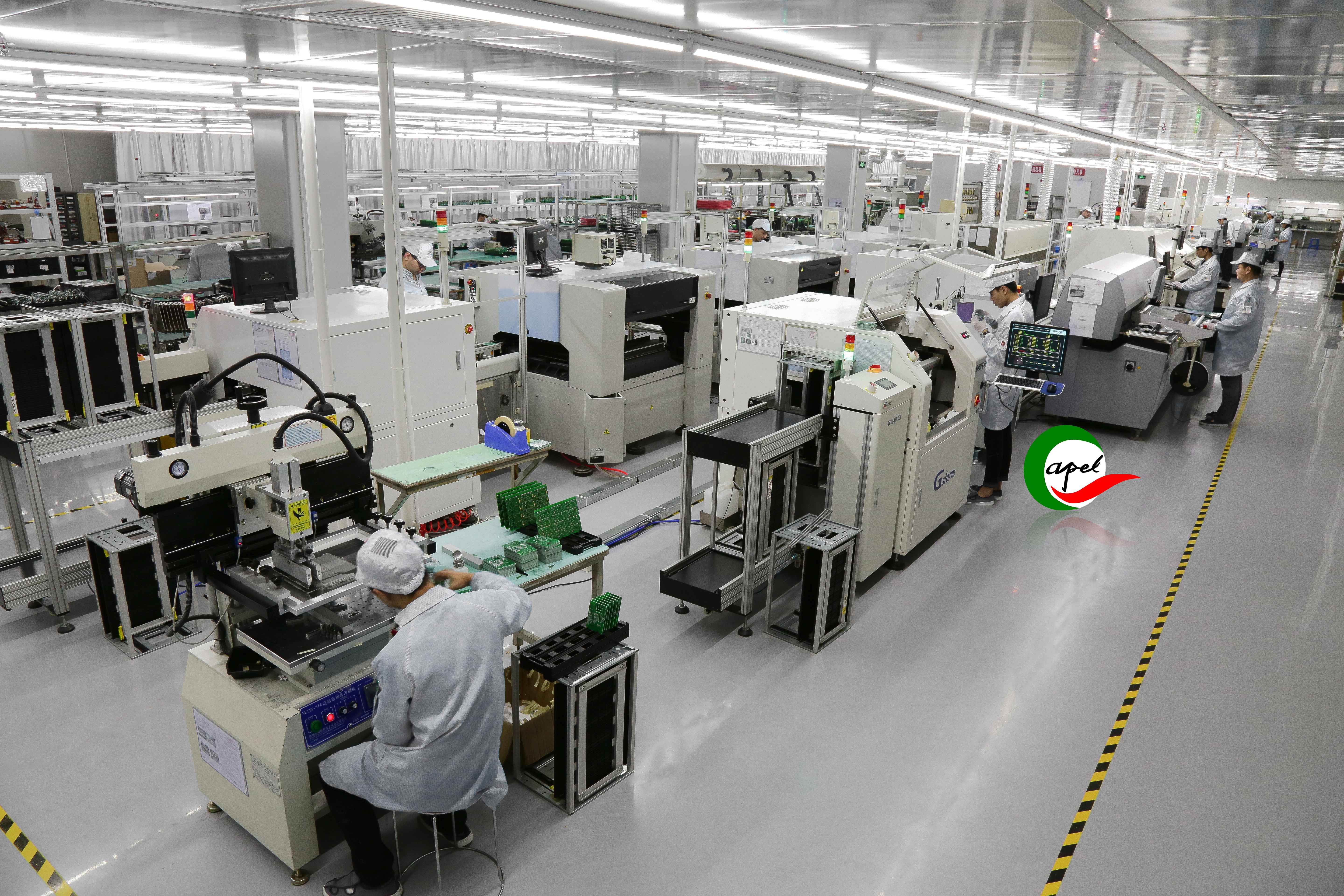